In today’s world, robots have permeated every facet of life, with automation becoming a cornerstone of industrial and commercial growth. Autonomous Mobile Robots (AMRs) and Automated Guided Vehicles (AGVs) are now vital in boosting productivity across various sectors, including industrial automation, agriculture, construction, retail intralogistics, and hospitality. These mobile robots address labor shortages and enhance operational efficiency, responding to an ever-expanding array of applications.
As companies continuously seek innovative technologies to tackle emerging challenges, AI-powered solutions are increasingly taking center stage, poised to play an even larger role in the future of robotics. This backdrop highlights the need for advanced solutions like Dusun IoT’s RK3588-based robot motherboard and controller, designed to meet the evolving demands of modern robotics applications.
“With the integration of the powerful RK3588 chipset, these new offerings deliver excellent computing power and versatility, aiming to cater to a wide array of applications, from industrial automation to various service robots.”
Xiang Wu, Dusun IoT product director
Basic Robotic Framework (Excluding Drones)
The mainstream robotics framework, excluding drones, is designed to integrate various advanced technologies to enable effective robotic functionality and interaction. At the core of this framework are SLAM algorithms. These algorithms, are often supported by chips from Intel and Qualcomm and implemented within ROS systems. Speech recognition algorithms and human-robot interaction play a pivotal role in seamless communication and interaction. Motion control is achieved using MCUs. This cohesive framework enables robots to operate efficiently across diverse applications.
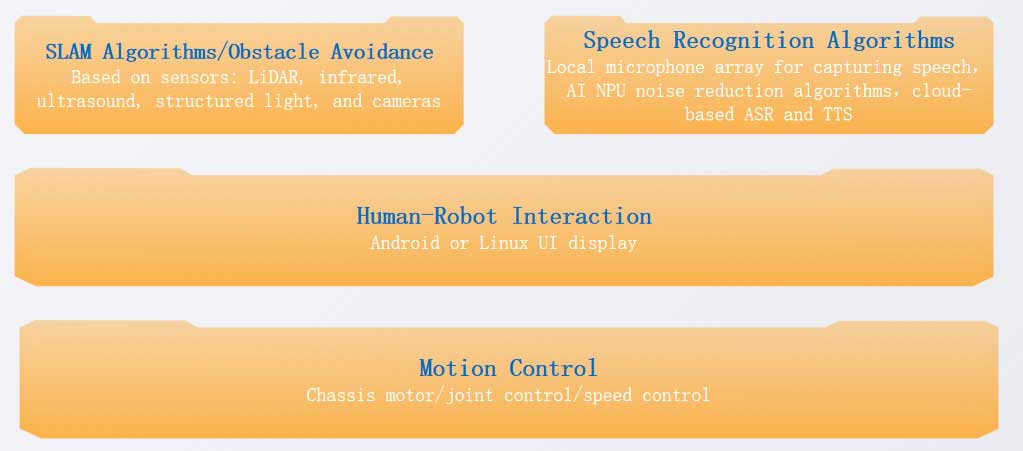
Perception and Mapping
SLAM Algorithms
- Function: Obstacle avoidance and robot perception.
- Sensors: LiDAR, infrared, ultrasound, structured light, and cameras.
- Hardware: Typically utilize chips from Intel and Qualcomm.
- Software: Commonly use ROS (Robot Operating System) for system integration and algorithm implementation.
Communication and Interaction
Speech Recognition Algorithms
- Input: Local microphone array for capturing speech.
- Enhancements: AI noise reduction algorithms to improve recognition accuracy.
- Cloud Services: Utilization of cloud-based Automatic Speech Recognition (ASR) and Text-to-Speech (TTS) for advanced processing.
Human-Robot Interaction
- Platforms: Android or Linux motherboards.
- Function: Facilitates robot UI display and human-computer interaction.
Motion Control
Motor and Joint Control
- Controllers: Microcontroller Units (MCUs) widely used.
- Purpose: Ensures fast responsiveness and precise control of motors and joints.
Challenges Faced by Robotic Embedded Hardware
The complexity of mobile robots is increasing rapidly, presenting challenges such as communication delays, algorithm iteration, and an escalating demand for computing power. To address these challenges, the robotics industry requires highly integrated embedded hardware solutions.
- Highly Integrated Solutions: Mobile robots demand embedded boards and controllers that are more comprehensive, aiming to reduce communication delays and enhance overall operational efficiency.
- Greater Computing Power Demand: With more industries integrating mobile robots into everyday operations, there’s a need for higher computing power to tackle complex situations. This drives the requirement for more powerful CPUs and NPUs.
- Versatile Applications: As mobile robots become ubiquitous across sectors, current motherboards must adapt to versatile applications and offer the flexibility to be customized for specific needs.
Introducing Dusun IoT’s RK3588-powered Robotic Motherboard and Controller Solutions
Dusun IoT offers a range of System on Modules (SoMs), embedded boards, and controller boxes powered by Rockchip, specifically designed for robotic applications. Our embedded hardware solutions are characterized by their compact size, low power consumption, and numerous interfaces, supporting a diverse array of robotic functions, including human-robot interaction, environmental perception, voice recognition, and motion control. These powerful solutions are ideal for developing various mobile robots, including hotel service robots, industrial AMRs and AGVs, robotic arms, delivery robots, mowing robots, and more.
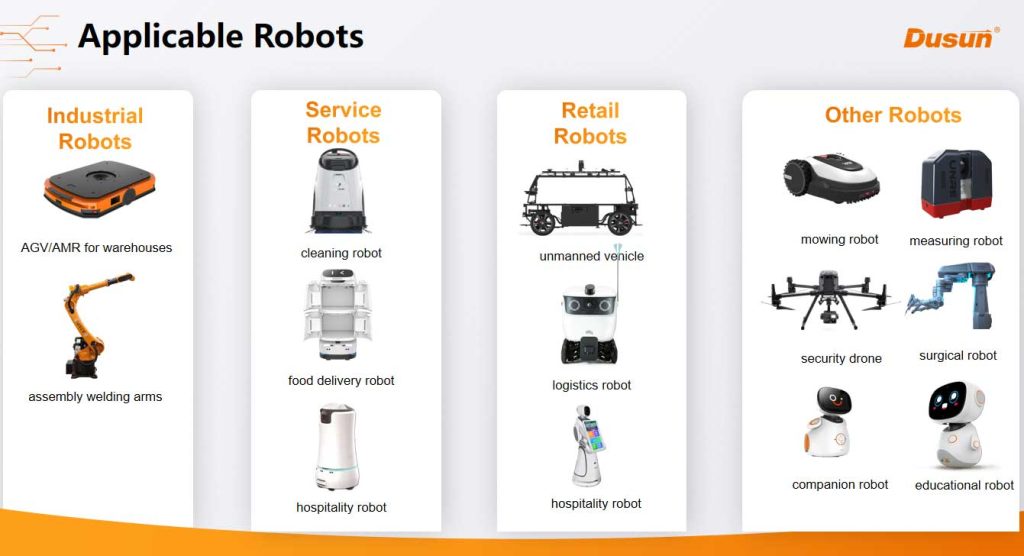
DSRP-010 Robotic Motherboard
DSRP-010 is an advanced embedded robotic motherboard that harnesses the power of the cutting-edge RK3588 chip. Featuring an octa-core CPU paired with an efficient NEON coprocessor, this motherboard boasts a built-in NPU capable of handling mixed operations with both integer and floating-point calculations. With an impressive performance of up to 6 TOPS, it delivers robust computing resources tailored for AI edge computing applications.
Designed to accommodate a wide range of connectivity requirements, DSRP-010 offers a diverse array of I/O interfaces, ensuring reliable performance across various operational environments. Its advanced deep learning capabilities and edge computing functions enhance data processing efficiency, reducing latency significantly.
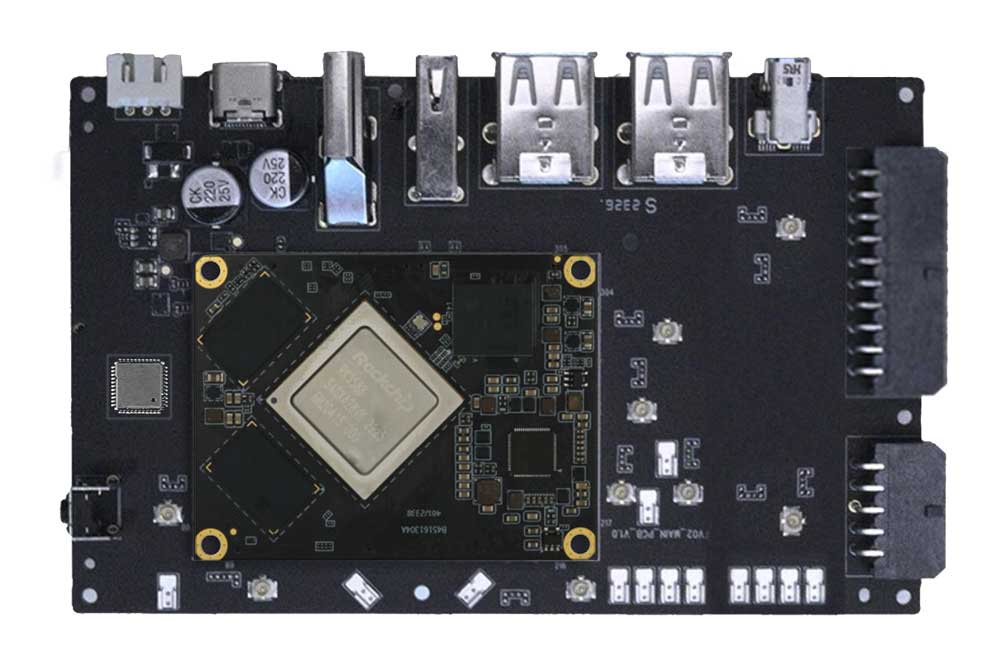
Key Features Include:
- Operating system support: Ubuntu20.04/ Android +LinuxRT(AMP multi-core Heterogeneous), support ROS and ROS2;
- 8 GB LPDDR4 and 64 GB eMMC; one SIM/TF card;
- Support 4G LTE CAT4 and reserve M.2 socket;
- Wi-Fi 5 and Bluetooth 4.2 Connectivity
- Integration with Industrial Bus Protocols such as CAN and RS485 (two ports for each)
- Multiple Isolated Interfaces: two DI, two DO, four AI, one IC, one I2S, two UART;
- One Gigabit Ethernet port;
- Versatile Video I/O Options: HDMI, LVDS, MIPI-CSI, and more
- Dual-Channel Audio Output: one 3.5mm line out, supporting re-collection and connection to MIC array (USB audio);
- USB: two USB 2.0 ports and two USB 3.0 Type A ports, one USB 3.0 OTG Type C port;
- Cooling method: Radiator self-heating
- Antenna: 3-way Ipex connector
Suitable Applications:
The DSRP-010 is ideal for a range of small robotic applications, including companion robots, lawn mowing robots, and robotic arms, making it a versatile choice for developers and engineers looking to innovate in the robotics space.
DSRB-010 Robotic Controller Box
DSRB-010 is a robust AI-powered robotic controller box, designed with the industrial-grade RK3588J core processor to ensure exceptional performance in demanding environments. Constructed from durable aluminum alloy, it features an integrated cooling system that maintains stable operation even under heavy loads.
Equipped with a wide range of standard interfaces such as HDMI, USB, and Ethernet, the DSRB-010 supports custom development tailored to specific operational needs. It comes pre-installed with a comprehensive SDK and Board Support Package (BSP) designed for the robotics industry, facilitating efficient human-computer interaction and mobile control, which in turn enhances the overall performance and reliability of the robotic system.
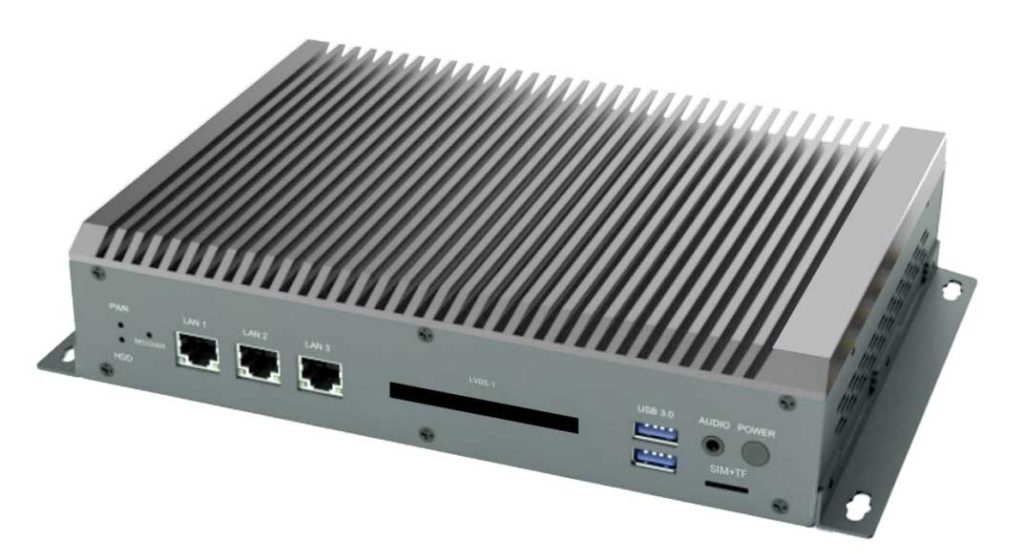
Key Specifications:
- Operating System Support: Ubuntu 20.04 / Android + LinuxRT with AMP multi-core heterogeneous processing; compatible with ROS and ROS2.
- Powerful Processing: 8 GB LPDDR4 RAM and 64 GB eMMC storage, with support for one SIM/TF card.
- Connectivity Options: 4G LTE CAT4, Wi-Fi 5, Bluetooth 4.2, and LoRa;
- Industrial Bus Protocols: Three CAN ports and one RS485 port;
- Multiple Isolated Interfaces: Includes one RS485 (DB9), one RS232 (DB9), two digital inputs, two digital outputs, and four analog inputs.
- Triple Gigabit Ethernet Ports;
- Versatile Video I/O: Options include HDMI, LVDS (with USB touch support), USB DP, and more.
- Dual-Channel Audio Output: One 3.5mm line-out and multiple USB ports, including four USB 2.0 and two USB 3.0 Type A ports.
- Cooling Mechanism: Efficient radiator self-heating design.
- Enhanced Signal Quality: Equipped with external rod antennas for improved connectivity—two for LTE (4G), one for Wi-Fi (2.4G/5G), one for Bluetooth, one for LoRa, and one for GPS.
- Industrial Standards: Operating temperature range of -40°C to 85°C.
Ideal Applications:
The DSRB-010 excels in a variety of scenarios, including AGVs, AMRs, service robots, logistics robots, and industrial automation, making it a versatile choice for developers looking to elevate their robotic solutions.
Highlights of RK3588-powered Robotic Motherboard and Controller Solutions
Based on Rockchip RK3588 CPU, Dusun IoT’s Robotic Motherboard and Controller Box integrate environmental perception, human-robot interaction, and motion control together, offering a comprehensive and high-performance platform for robotics applications.
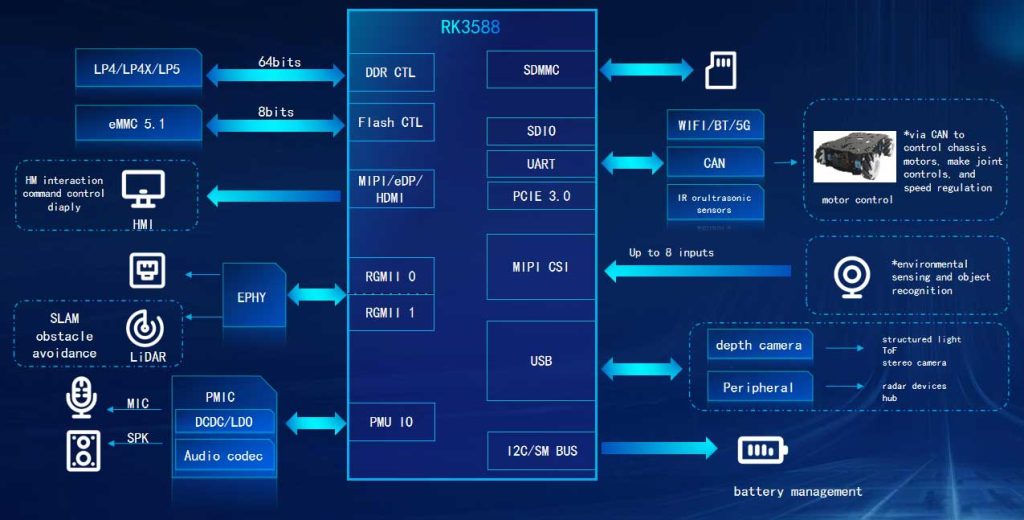
Environmental Perception
Designed with Android Subsystem for Linux (ASL) architecture, this solution supports built-in ROS/ROS1, enabling swift adaptation of SLAM algorithms.
With dual 8-channel digital microphone arrays, it leverages advanced AI-powered NPU voice algorithms, including noise reduction, sound optimization, howling suppression, voice activation, and keyword recognition, ensuring precise and effective auditory perception.
Human-Robot Interaction
The powerhouse combination of a Quad-Core A76 and Quad-Core A55 CPU delivers up to 93K DMIPS of computing prowess, while the G610 MP4 GPU provides an impressive 512 GFLOPs for graphics processing. Equipped with a triple-core NPU boasting 6 TOPS (INT8) computing capability, this system excels in AI tasks, achieving 59.6 fps on the yolo-v8n model.
The solution also offers versatile video output through MIPI, Type C, eDp, and HDMI, and supports an impressive 7-screen display configuration.
Motion Control
Supporting AMP multi-core heterogeneity, this system allows simultaneous operation of the human-machine interaction layer (Android/Linux) and the mobile control system (RTOS). It achieves microsecond interrupt response times, meeting the stringent real-time and stability demands of robotic applications with exceptional efficiency and precision.
Also read: The Feasibility of Using RK3588J to Build Robot Control Board
Final Words
Dusun IoT is committed to delivering top-tier System on Module (SoM) and motherboard products, coupled with sustainable manufacturing practices. From initial concept and design to hardware and software development and parts procurement, our fast and knowledgeable technical support makes us your go-to partner for industrial-grade intelligent modules.
Our standard robotic controller boxes can be customized to meet specific needs, including adjustments in size, interface configurations, and peripheral sensors. Additionally, for robotic SoMs and motherboards, we provide ODM and JDM services, tailoring embedded hardware to fit unique requirements. Regardless of whether you choose SoMs, motherboards, or controller boxes, we provide comprehensive SDKs and BSP development support tailored to the robotics industry.
Our cutting-edge robotic solutions are designed to empower you in developing versatile applications while minimizing the resources needed during the prototyping phase. We offer tools that seamlessly integrate with diverse development environments and support AI engines, ensuring maximum flexibility and expandability. With a streamlined integration path for sensors, actuators, and other I/Os, Dusun IoT is here to help you realize your innovative robotic visions.
FAQs
How to use AI for object detection?
To facilitate effective obstacle detection and collision avoidance, AMRs and AGVs usually utilize advanced high-resolution cameras, including structured-light RGBD and Time-of-Flight (ToF) cameras. These cameras capture depth and intensity images at high frame rates, enabling AI algorithms to perform data fusion and object detection seamlessly, thus allowing robots to operate efficiently during their tasks.
For real-time navigation and spatial awareness, modern techniques like Simultaneous Localization and Mapping (SLAM) employ 2D and 3D Lidar systems, or camera-based approaches known as Vision SLAM.
Also read: Robot vision and AI algorithms
How to create a reliable processing module for mobile robots?
Designing a dependable processing module is essential for the effective operation of AMRs and AGVs. Key considerations include:
Adequate Computing Power: Ensure your module can handle the computational demands of autonomous navigation, object detection, path planning, and decision-making.
Cost-Effective Camera Connectivity: Implement methods to efficiently connect multiple high-resolution cameras via MIPI-CSI.
Ample Memory: Design the system with sufficient memory to store and process large data sets, such as sensor readings and mapping information, while running complex algorithms.
Versatile Connectivity: Include a range of interface options for sensors, actuators, and communication modules, incorporating both digital and analog I/O ports, as well as serial communication standards like UART, SPI, and I2C, alongside Wi-Fi connectivity.
Durable Construction: Use industrial-grade components to create a robust design capable of withstanding diverse conditions, including temperature fluctuations, dust, and vibrations, to ensure consistent performance.
Energy Efficiency: Prioritize power management features to optimize energy use, which is crucial for mobile robots that operate on battery power.
How to choose between system on modules and single board computers for mobile robot development?
SoMs offer a compact design that can be tailored to specific applications, maximizing cost efficiency. They provide configurable options for both software, through a Board Support Package (BSP), and hardware components like memory and I/O interfaces. SoMs often include evaluation kits that enable software development to start before finalizing the robot’s hardware, accelerating the path to market.
SBCs are ideal for large-scale production due to their cost-effective design. They include system design services that help expedite the development process and come with BSPs optimized for the hardware they support. SBCs typically run on Linux operating systems, with support from Debian, Yocto, and Buildroot distributions.
What advantages do mobile robots like AMRs and AGVs offer?
Dependable Workforce
Mobile robots provide a reliable workforce that does not experience fatigue. They can consistently operate to meet production targets, leveraging AI to enhance their precision and flexibility. This makes AMRs not only more accurate than human workers but also capable of performing complex tasks effectively over long periods.
Enhanced Safety
Equipped with advanced sensors and cameras, AMRs navigate their environments with ease, thanks to AI programming. This technology enables them to avoid obstacles—including products, infrastructure, and personnel—while moving throughout a facility. Additionally, AMRs can safely operate in high-risk, unmanned environments, such as chemical or nuclear facilities, significantly reducing the threat to human workers.
Lower Operational Costs
Incorporating AMRs into a workplace can lead to substantial reductions in labor costs, particularly for repetitive and labor-intensive jobs. With their ability to simultaneously handle multiple tasks at a faster pace, AMRs significantly boost efficiency, enabling organizations to allocate resources more effectively and enhance overall productivity.